Material Extrusion additive Manufacturing of metal parts
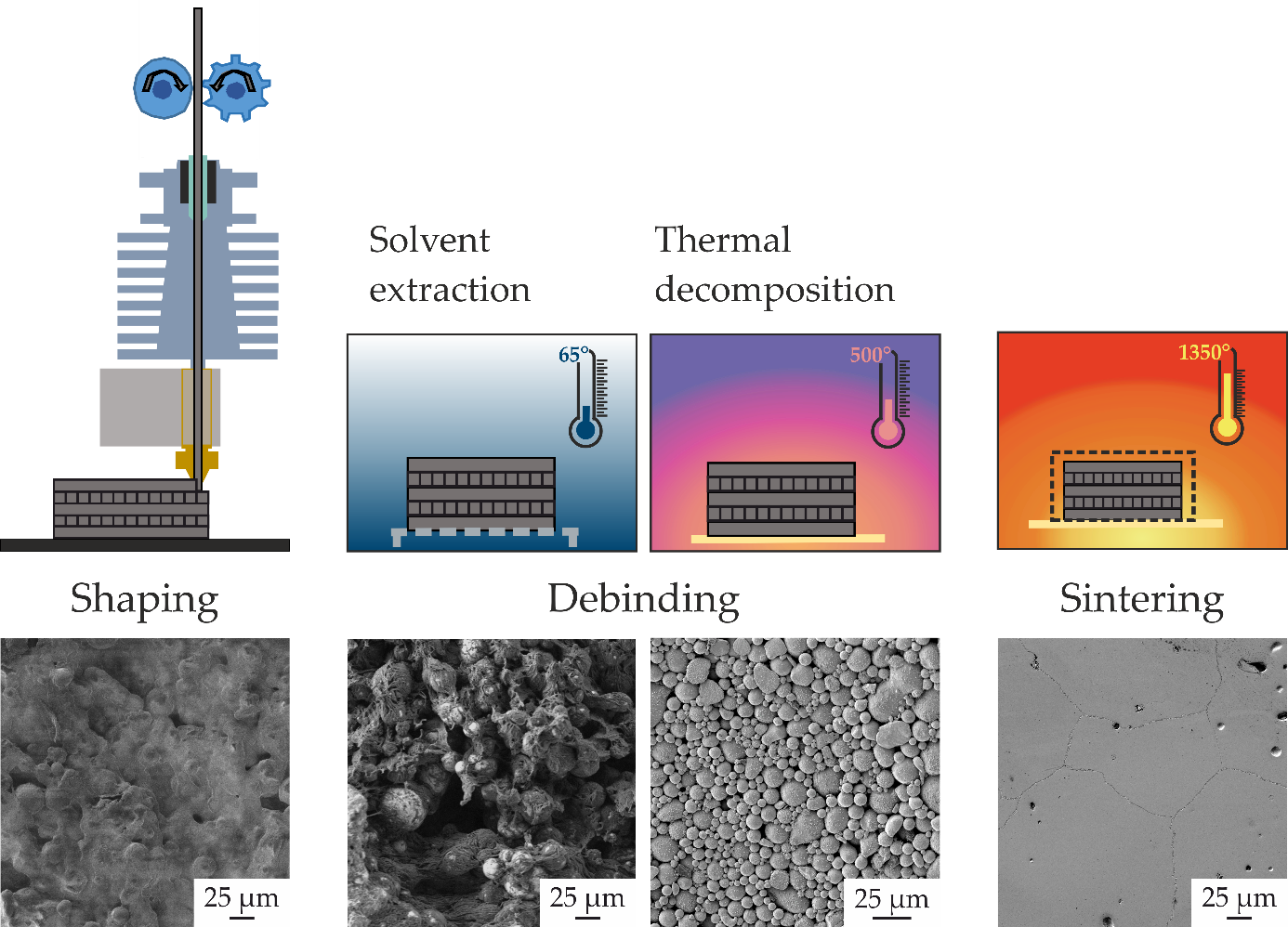
Additive manufacturing via filament extrusion, debinding and sintering of highly filled polymers is a cost-effective and material-flexible alternative to powder bed additive manufacturing processes for smaller metallic components. Complex components with attractive mechanical properties can be manufactured with significantly reduced system and material costs compared to beam-based processes. In addition, the comparatively slow heating and cooling rates make it possible to process materials that tend to cracking in conventional additive manufacturing. The process includes the shaping by filament extrusion of a filament filled with metal powder (> 55 % by volume), which can be realized in 3D printers for plastic extrusion. This is followed by a two-stage debinding process in which first of all the main component of the binder system is chemically extracted. The remaining backbone polymer still guarantees the dimensional stability of the green body before it is decomposed and removed in the subsequent furnace process. To maintain the shape during thermal debinding, the heating rate in the area of polymer decomposition must be greatly reduced in order to avoid the formation of defects due to increasing pressure inside the sample. The sintering for the final densification of the metal part takes place directly afterwards in the same furnace, whereby the temperature and sintering time must be optimized to achieve high final densities. Due to the filament-based shaping, this process can be used for the additive manufacturing of various metals such as copper, titanium, tool steels or superalloys. The parameter optimization during the different process steps as well as the choice of the furnace atmosphere are decisive for the achievable final density and have a decisive influence on the microstructure and the functional properties of the manufactured components.